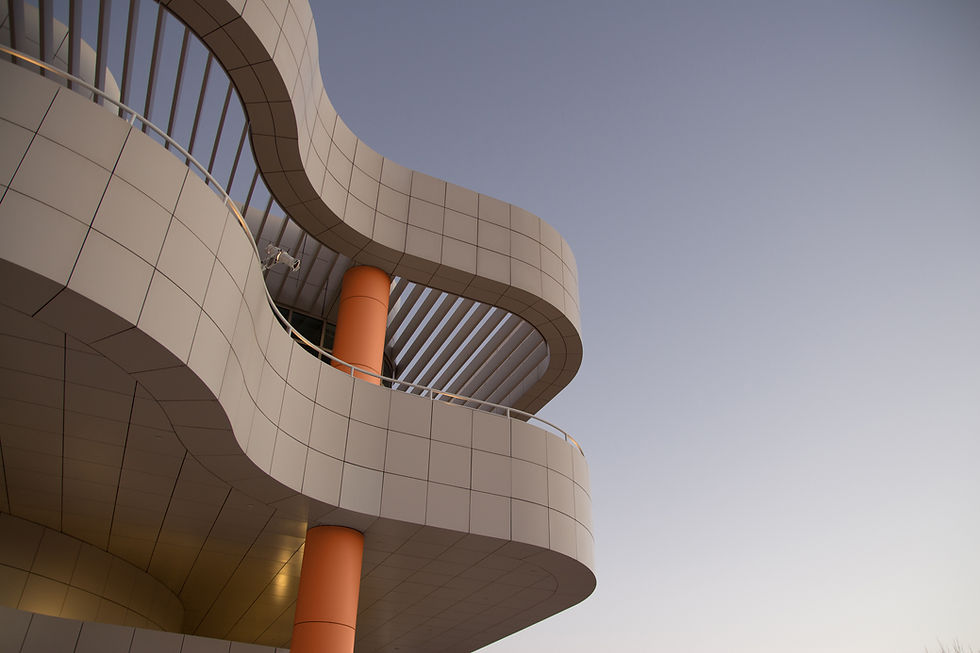
Stretch Wrapper Troubleshooting Basics
Jul 7, 2024
3 min read
0
7
0

Stretch wrappers are an essential piece of equipment in any warehouse or distribution center. They are used to secure and protect pallets of products during transport and storage. However, like any machinery, stretch wrappers can encounter issues and require repair. In this blog post, we will outline the general procedure for repairing a stretch wrapper.
1. Identify the problem
The first step in repairing a stretch wrapper is to identify the problem. This could be anything from the machine not turning on, to issues with the stretch film not wrapping correctly. It is important to closely examine the machine and determine the root cause of the problem. This will help in selecting the appropriate solution and parts for the repair. Depending on the issue, this can involve inspecting the mechanical components, or using a multimeter to check electrical components
2. Consult the manual
Most stretch wrappers come with a user manual that outlines the machine's parts, functions, and troubleshooting steps. Before attempting any repairs, it is important to consult the manual for guidance. The manual may also include a list of common problems and their solutions, which can be helpful in identifying the issue.
3. Gather necessary tools and parts
Once the problem has been identified, it is essential to gather the necessary tools and parts for the repair. This could include replacement parts, such as belts, motors, or sensors, as well as tools such as screwdrivers, wrenches, and pliers. Having all the necessary tools and parts on hand will save time and ensure a smoother repair process.
4. Disconnect power source and remove covers
Safety should always be a top priority when repairing any machinery. Before beginning any repair work, make sure to disconnect the stretch wrapper from its power source. This will prevent any accidents and allow for a safe repair process. Once the power has been disconnected, remove any covers or guards that may be obstructing access to the problem area.
5. Replace or repair damaged parts
If a part is damaged or broken, it will need to be replaced. This could include belts, motors, sensors, or other components. Refer to the manual for instructions on how to properly replace the damaged part. If the part cannot be replaced, it may need to be repaired. In this case, follow the manual's instructions or seek professional assistance.
6. Test and calibrate the machine
Once the damaged parts have been replaced or repaired, it is important to test the machine to ensure it is functioning properly. Reconnect the power source and run a few trial runs to check if the issue has been resolved. If the issue persists, the machine may need to be recalibrated. Follow the manual's instructions for calibrating the machine correctly.
7. Regular maintenance and upkeep
Prevention is always better than cure. Regular maintenance and upkeep of the stretch wrapper can help prevent future issues and prolong the machine's lifespan. This includes keeping the machine clean, checking for any wear and tear on parts, and replacing them when necessary. It is also important to follow the manufacturer's recommended maintenance schedule to keep the machine running smoothly.
In conclusion, repairing a stretch wrapper requires a systematic approach and attention to safety measures. Identifying the issue, consulting the manual, gathering necessary tools and parts, and conducting proper maintenance can help in keeping the machine running smoothly. In case of complex issues, it is always best to seek professional assistance. With proper care and maintenance, a stretch wrapper can continue to efficiently and effectively secure pallets for years to come.
If you have an issue that you are struggling to figure out, please reach out to us! Our technicians are fluent in common repairs and issues with stretch wrappers, and are happy to come out and help fix your equipment. We can be reached by phone at  (910) 239-7564 or email at service@mortonsmachine.com.